Investing in timely stretch wrap machine repair can lead to better wrapping performance.
Investing in timely stretch wrap machine repair can lead to better wrapping performance.
Blog Article
A Comprehensive Strategy to Dealing With Stretch Wrap Machine Fixing Obstacles
You know that stretch wrap equipments are essential for preserving effectiveness in product packaging operations. Concerns can occur that interrupt efficiency. What are the best approaches to guarantee your devices run efficiently?
Understanding Usual Stretch Wrap Machine Issues
When you depend on stretch wrap makers for efficient product packaging, it's essential to identify usual concerns that can disrupt operations - stretch wrap machine repair. One widespread problem is inconsistent tension, which can lead to insufficient wrapping and endangered load security. If you discover the film isn't adhering correctly, look for worn-out rollers or inappropriate settings
Another issue you may deal with is movie breakage, typically caused by wrong movie type or device malfunctions. On a regular basis check the equipment for signs of damage to avoid this.
In addition, watch on movie build-up or jams, which can halt manufacturing. Commonly, this occurs due to misalignment or debris in the device.
Last but not least, improper sealing can cause loads coming apart throughout transportation. Ensure your machine is adjusted properly to preserve the stability of your plans. By staying alert and attending to these issues promptly, you can help with smoother operations.
The Relevance of Routine Preventative Upkeep
Regular preventive upkeep is vital for maintaining your stretch wrap device running efficiently and successfully. By regularly checking and servicing your devices, you can detect potential issues before they escalate right into expensive repair services. This positive technique not just extends the life expectancy of your equipment but also ensures that it runs at peak performance.
You should set up regular evaluations to tidy, lubricate, and replace worn components. Keeping your machine calibrated aids maintain excellent wrapping high quality, reduces waste, and improves productivity. Furthermore, recording upkeep tasks creates a reputable history that can notify future decisions.
Don't forget the significance of training your team on upkeep ideal practices. When everyone comprehends just how to take care of the equipment, you decrease the risk of driver mistake bring about malfunctions. In short, committing to routine preventative maintenance is a smart investment that repays in reduced downtime and enhanced performance in your operations.
Fixing Strategies for Quick Services
Reliable fixing techniques can significantly decrease downtime when your stretch wrap maker runs into problems. Begin by identifying the symptoms. Is the device not covering properly or is it making uncommon noises? Once you have actually identified the problem, refer to the operator's handbook for assistance on typical concerns and options.
Next, examine the machine's setups and controls; often, a straightforward modification can solve the issue. Examine the movie tension and alignment, as incorrect arrangement can lead to covering failures. Don't forget electrical connections; loosened or broken wires can interfere with performance.
If you're still facing difficulties, consider running diagnostic examinations if your device has that ability. Don't hesitate to consult with a service technician if you can't settle the issue swiftly.
Training Operators for Effective Device Usage
To ensure your stretch cover equipment runs at peak effectiveness, proper training for drivers is necessary. When operators recognize the equipment's performances, they can optimize its potential and lessen downtime.
Encourage them to practice under guidance, resolving any kind of inquiries or problems they might have. On a regular basis arranged refresher courses can maintain their skills sharp and assist them adapt to any type of updates or changes in technology.
Additionally, infuse a culture of accountability by empowering drivers to report concerns or suggest enhancements. This positive method not just boosts their self-confidence yet also contributes to the overall efficiency of your procedures. With well-trained drivers, you'll see fewer errors and enhanced performance, ensuring your stretch cover machine continues to be an important property.
Constructing a Solid Interaction Channel Between Teams
Trained operators can only execute at their best when there's a solid communication network in between groups. Effective interaction removes misconceptions and guarantees every person's on the very same page relating to maker procedures and repair service needs. Motivate normal check-ins and conferences to talk about concerns, share insights, and address problems.
Using innovation, like messaging apps or collaborative systems, can enhance real-time interaction, making it less complicated to report troubles and share updates quickly. Appointing clear roles and obligations promotes accountability, permitting employee to connect to the right individual when problems emerge.
Furthermore, developing an open environment where every person feels comfortable sharing responses can lead to cutting-edge remedies. By focusing on interaction, you're not just enhancing maker efficiency; you're also constructing a cohesive team that collaborates seamlessly. This collective spirit inevitably brings about quicker repair services and lowered downtime, benefiting the entire operation.
Purchasing Top Quality Substitute Components
When it concerns preserving your stretch cover machines, purchasing quality substitute parts is crucial for making sure trustworthy efficiency and reducing downtime. Inexpensive options might seem alluring, yet they usually result in more considerable concerns down the line, costing you much more in repair work and shed productivity. By selecting top quality components, you're not simply dealing with an issue; you're enhancing the total efficiency of your equipment.
Additionally, quality components are generally made to stricter criteria, which means they'll fit much better and operate more dependably. This reduces the probability of unforeseen malfunctions, allowing your operations to run smoothly. Moreover, reliable distributors often provide service warranties, giving you assurance in your investment.
.jpg)
Examining Performance Data for Constant Renovation
To enhance your stretch cover maker's efficiency, you require efficient data collection techniques. By reviewing performance metrics, you can pinpoint locations for renovation and increase effectiveness. Determining these opportunities not just streamlines procedures yet additionally minimizes downtime and repair work prices.
Data Collection Methods

Efficiency Metrics Evaluation
While examining efficiency metrics, it's essential to focus on particular data factors that straight affect your stretch cover maker's efficiency. Start by tracking cycle times, as they expose just how swiftly your equipment operates under normal problems. Screen downtime occurrences to recognize patterns or reoccuring problems that may need dealing with. Maintain an eye on movie use, guaranteeing you're not wasting product, which can impact prices and performance. In addition, evaluate result high quality by examining for inconsistencies in the covering process. By analyzing these metrics regularly, you can pinpoint areas requiring attention and take positive procedures. This continuous analysis aids improve productivity, lower expenses, and eventually improve your device's longevity, causing a more effective wrapping operation on the whole.
Identifying Renovation Opportunities
As you assess efficiency data, you can reveal beneficial enhancement opportunities that enhance your stretch wrap maker's effectiveness. Look for patterns in downtime, cycle times, and cover top quality. If constant failures associate with specific operating problems, you can readjust procedures to minimize these problems.
Often Asked Questions
How Can I Inform if My Equipment Needs a Repair Service or Just Maintenance?
To tell if your device requires fixing or just upkeep, listen for uncommon noises, look for inconsistent efficiency, and evaluate for visible wear. If problems persist after maintenance, it's most likely time for a repair service.
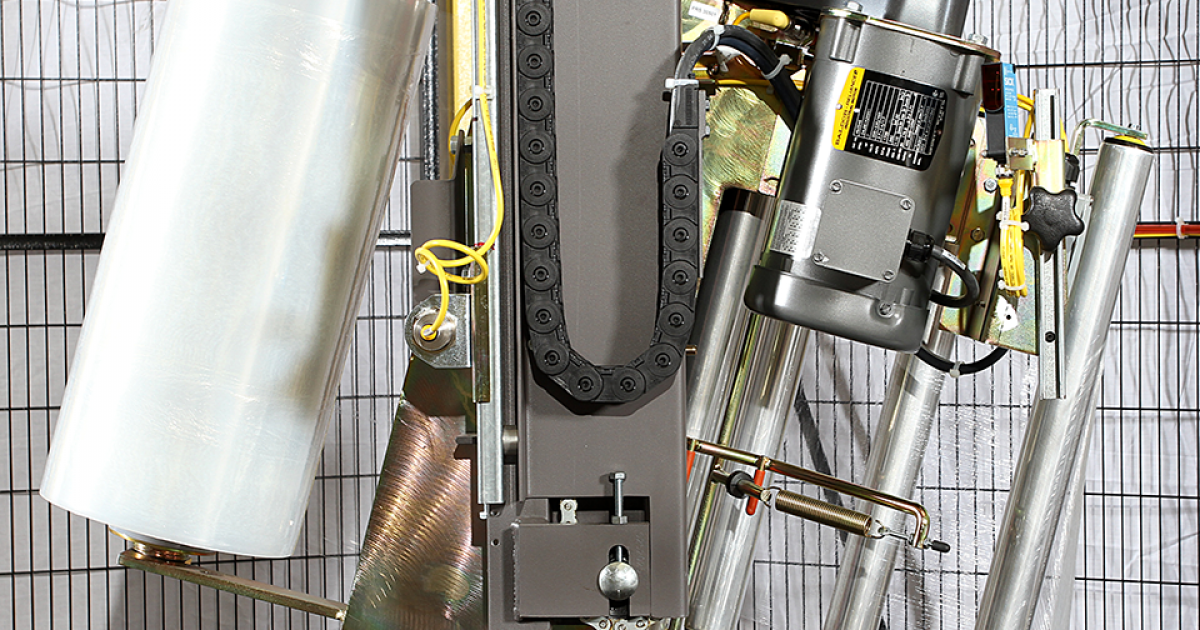
What Is the Ordinary Lifespan of a Stretch Cover Machine?
The average life-span of a stretch wrap device is normally five to 10 years, depending upon usage and upkeep. Routine treatment can prolong its life, so maintain an eye on efficiency and address problems additional resources without delay.
Exist Details Brand Names Understood for Better Integrity?
Yes, some brand names are known for their dependability. You'll discover that business like Signode and Lantech often get favorable evaluations - stretch her latest blog wrap machine repair. Researching user feedback can assist you pick a dependable stretch cover machine for your needs
What Are the Indications of Poor Operator Training?
If you see frequent errors, inconsistent wrapping, or security cases, those are signs of bad operator training. Absence of understanding about maker features or failing to follow methods can greatly affect efficiency and security.
Just How Can I Discover a Professional Specialist for Repairs?
To discover a qualified specialist for fixings, request suggestions from sector peers, check on-line testimonials, and validate certifications. You might also take into consideration contacting local equipment distributors that frequently have relied on technicians handy.
Final thought
To summarize, tackling stretch cover maker repair work difficulties calls for a positive approach. By prioritizing precautionary upkeep, supplying detailed driver training, and investing in top quality parts, you can significantly reduce downtime and improve performance. Don't neglect the importance of solid communication between groups and constant assessment of maker output. By applying these approaches, you'll not only improve covering high quality but likewise promote a society of effectiveness and enhancement in your operations. Stay in advance of concerns prior to they arise!
Report this page